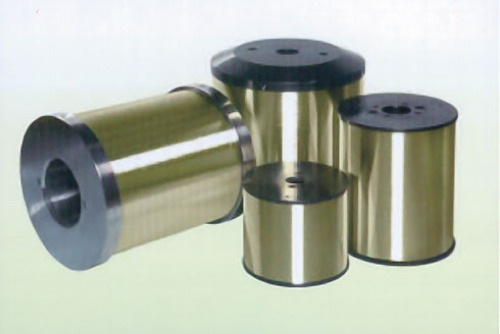
As an inexhaustible source of clean energy, the development and utilization of solar energy has attracted more and more attention in the industry. Solar cells are mainly produced using non-toxic crystalline silicon. Monocrystalline and polycrystalline silicon cells are characterized by high photoelectric conversion efficiency, long life, and good stability, but the cost is high. With the continuous maturity of semiconductor manufacturing technology, the manufacturing cost of silicon wafers continues to decrease, but the cost of cutting silicon wafers used in solar cells has remained high, accounting for more than 30% of the total manufacturing cost of solar cells. Cutting wire used for cutting silicon wafers and wire rods for cutting steel wires are important components in the photovoltaic industry chain.
For China's wire rods for cutting steel wire, it is only at the stage of exploration and start-up. Although China's photovoltaic industry is affected by many factors such as external economic environment and industry competition, it is at a stage of difficult restructuring and repositioning. However, with the end of the industry reshuffle, China's "spring" cutting wire and wire rod will come. With the continuous improvement of the quality of wire rods for cutting steel wire in China, China's cutting wire for photovoltaic products is expected to use all domestic wire rods.
Cutting wire has broad application prospects. China is a global producer of photovoltaic modules, and crystalline silicon cutting is a key technology for crystal silicon processing in the solar photovoltaic industry chain. Therefore, the application prospect of cutting steel wire is very promising. Related data shows that 1MW crystalline silicon solar cells require 12 tons of crystalline silicon, and each ton of crystalline silicon requires 0.7 tons of cut steel wire.
Since silicon wafers are expensive ($60/kg), the cutting process must accurately balance and control the wire diameter, cutting speed, and cutting area to ensure that wafers are produced. This ensures that wafers are not cut in the shortest cutting time. Broken, uniform thickness of silicon wafers. Therefore, the cutting steel wire must be under very fine specifications (0.07mm~0.2mm), and the pass is even, with high tensile and fatigue strength.
According to reports, Bekaert is the world’s first manufacturer to enter the field, once monopolized the cutting wire market in the early days. China also has a number of companies involved in the field of cutting steel wire, such as the professional production of cutting wire manufacturers Zhenjiang resistance wire, Changzhou Fandeng based on the special steel wire market, has involved in cutting steel wire. (Please refer to the attached table for the domestic partial cut wire manufacturers and their production capacity in China)
The production of cutting wire products is difficult and the finished product rate is low. At the same time, there are usually relatively strict compensation regulations between cutting wire manufacturers and silicon wafer manufacturers. For example, if a wire break occurs during the slicing process at a silicon wafer mill, the cutting wire manufacturer must not only compensate for the cutting wire. This part of the loss, but also for the loss due to broken silicon wafers caused by the damage caused by the loss. Therefore, the cutting wire itself is priced higher. When the market price is high, the unit price of cutting steel wire is 9 yuan/meter to 12 yuan/meter, and after conversion is about 10 yuan/ton.
Cutting wire is divided into copper-plated cutting wire and diamond cutting wire. At present, the domestic use of copper-plated cutting steel wire, its advantage is the low cost of cutting steel wire, the disadvantage is poor production efficiency, high demand for cutting fluid, pollution, and need to be replaced. Ganggang cutting steel wire is coated with a layer of wear-resistant emery particles on the surface of the cutting wire, without cutting fluid, can be directly cut, its advantages are high production efficiency and product rate, can be used repeatedly, the disadvantage is that the unit price of steel is expensive, at present in China Popularity, the Japanese market uses this product in part.
The quality of wire rods for cutting steel wires needs to be improved due to good market demand, development prospects and higher profitability (as compared with other wire rods), as well as the investment in equipment and technology of iron and steel enterprises and wire rod production technology for cords in recent years On the breakthrough, China's large and medium-sized steel mills and wire rod specialists have all developed and developed wire rods for wire cutting. However, on the whole, China's wire rods for cutting steel wire are not used as wire rods for cords. They are used for cutting steel wire products in batches. There is still a gap between the requirements of users and the quality of imported wire rods.
The commonly used steels for the production of wire rods for cutting steel wire are high-carbon wire rods with a carbon content of 0.85% to 0.9%. The chemical composition and basic properties are similar to those for cords. However, because the product is different from the cord, the cord product is used after the tantalum strand, and the cutting steel wire is used in the form of a monofilament. Therefore, there is a higher requirement for the inclusion and the stripe nature of the rod and the crystal phase organization. Currently, there are only steel mills capable of stably mass-producing wire rods for cutting around the world. They are Germany-based Sasset, Japan's Nippon Steel & Sumitomo, and Japan's Kobe Steel. Except for Nippon Steel's live wire rods, which have ** cutting wire, the other wire rods are universal. In terms of market share, 80% of Kobe Steel, 12% of Sasita, and 8% to 15% of Nippon Steel lived in gold.
According to the author's understanding, the companies that currently develop wire rods for cutting wire rods are all steel companies that produce wire rods for cords, such as Baosteel, Wuhan Iron and Steel, Anshan Steel, Qinggang, Xingtai, Nangang and Shagang. In order to better penetrate the downstream industries, Baosteel and Xing Steel also invested in the establishment of a professional production line for cutting steel wire. Baosteel's wire rods for cutting steel wires have been tested in batches into cutting wire companies.
Relevant data show that Japanese wire rods for wire cutting adopt fine management mode for the production of raw materials, auxiliary materials and production status: raw material selection of tri-ferrice and high-quality scrap (strict control of residual elements), accessories on the size, quantity, manufacturers, add Processes are strictly controlled. When the iron and steel enterprises in China formulate technological processes, these aspects are also strictly regulated, but they often appear to be biased when they are actually implemented. This is where domestic companies must focus and improve.
Coexistence of Challenges and Opportunities According to surveys conducted by relevant parties, more than half of China's small and medium-sized battery module companies have stopped production, 30% have sharply reduced production, and 10% to 20% have reduced their output by a small amount or they are striving to maintain their production and operations. However, some unfavorable factors faced by enterprises have also inhibited the development of wire rods for wire cutting and wire cutting, and the enthusiasm of related companies has also weakened.
First of all, China's photovoltaic products are highly dependent on the international market. China's current PV product export ratio has been above 95%, resulting in unbalanced domestic and foreign markets for photovoltaic products, which is extremely unfavorable to the foreign trade of photovoltaic products in China. Second, the domestic production capacity in the first phase blindly expanded. At present, China's photovoltaic-related products have experienced serious oversupply, and the same applies to wire rods and wire rods for cutting steel wires. Cutting steel wire manufacturers have significantly reduced the price of cutting steel wire in order to sell their products, which has recently reached 23,000 yuan/ton, which is far below the price level in the first half of 2011, but has not achieved the expected sales effect. Finally, the tension in the capital chain limits development. Affected by the slowdown in China's economic growth, there have been varying degrees of tension in the capital chain of many domestic steel wire cutting and related companies.
At the same time, companies should also be aware of the existence of industry opportunities.
The original intention of the country to develop clean energy remains unchanged. Compared with traditional power generation methods, photovoltaic power generation has become the direction of future development due to its clean and other characteristics, and it is also a project that countries around the world will support and encourage for a long time. In the “Twelfth Five-Year Planâ€, the Chinese government proposed a plan to support the development of clean energy. For example, in order to promote domestic photovoltaic applications, China has successively introduced a number of policies and carried out a number of demonstration projects, such as demonstration projects for the integration of photovoltaic solar building applications. In 2011, the “Notice of the On-grid Electricity Tariff Policy for Solar Photovoltaic Power Generation†issued by the National Development and Reform Commission confirmed the national benchmark price, which is a milestone significance for domestic photovoltaic applications.
The reduction in processing costs has accelerated the civil progress. For domestic photovoltaic power generation, the high cost of grid-connected power generation due to the high manufacturing costs of each link. However, as the price of cutting steel wire is drastically reduced and the domestic wire cutting industry and market are further standardized, the use cost of photovoltaic power generation in China is gradually reduced, which may bring about the possibility of large-scale photovoltaic power generation and use in China.
We supply full range of abrasive tools, such as Flap Disc adhesive, Flap Disc Backing Pad, Abrasive Flap Disc, Flap Wheels , flap wheel with shaft, Abrasive Sanding Disc, Abrasive Machine , etc...
both one component epoxy adhesive and two component epoxy adhesive.
Specifications for single component epoxy adhesive for flap disc:
Appearance: Colloidal
Color: Blue / White
Odour: Slight odour
Proportion(water=1):1.42
Viscosity (25℃, mpa.s): 15000~20000
Storage time: 5℃ 6 months
Recommended curing condition: 110~130℃×4~3 hours or 150~160℃×1 hour
Hardness(Shore D): ≥90
Recommended temperture on the machine: 40-52 degree
Shearing strength(23℃, steel/steel, MPa): ≥22
Flap Wheel Glue Instructions
According to the ambient temperature, preheat adhesive among 41 ~ 46℃ before pumping into the pumping system.
Note:
1.When climate is colder, adjust preheating temperature 3 ~ 5℃ higher than normal.
2.Before use large quantities,a small quantity should be used for test.
3.This flap disc glue is a chemical product, can cause weak corrosive to skin, please note that the use of the appropriate protection, such as inadvertent contact with the skin with plenty of water rinse or alcohol wash.
4.Baking temperature is particularly important for product quality. The data provided by us is tested under accurate oven temperature control. We are strongly advised customer should adjust oven temperature according to the customer's on site condition.
Storage and transportation
Flap Disc Adhesive resin glue should keep in cool, ventilated warehouse, temperature does not exceed 40℃, relative humidity of not more than 85% ,this product is not special goods, according to the general cargo transport.
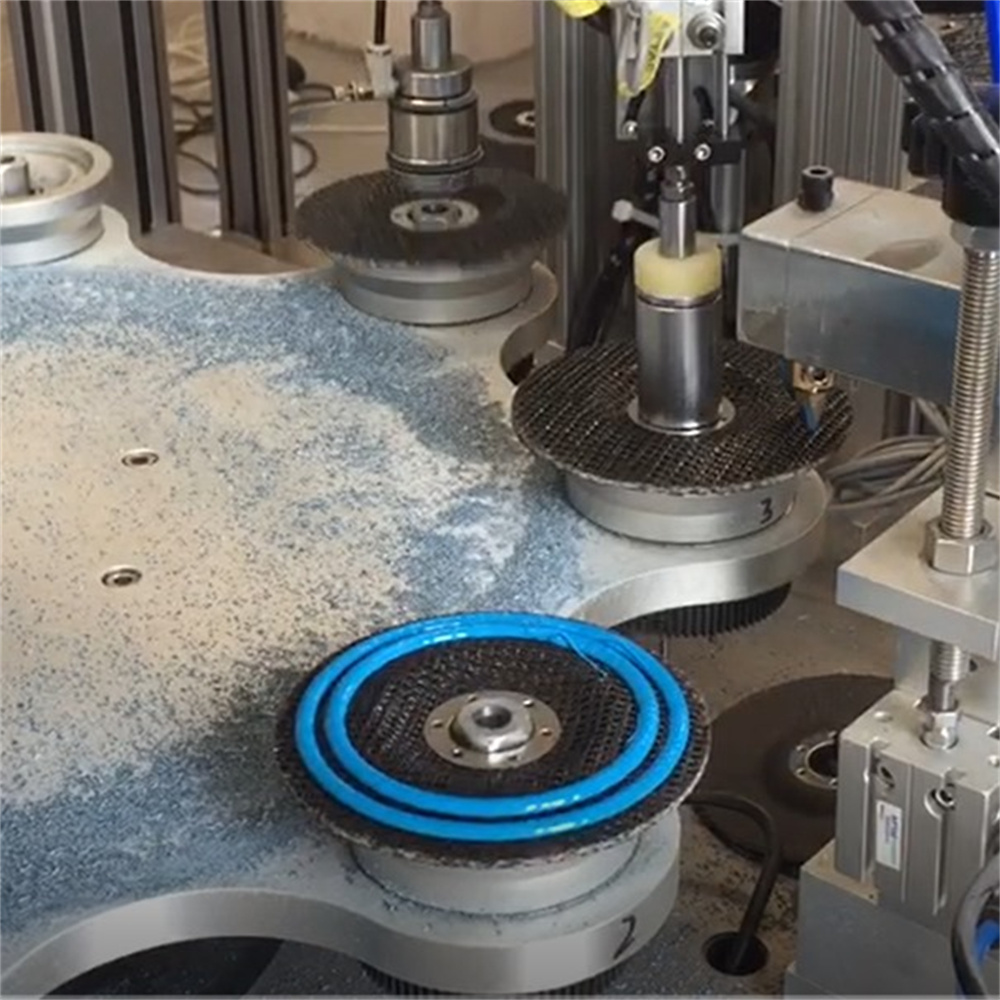
Flap Disc Adhesive Glue,Flap Wheel Glue,2 Component Epoxy Glue,Flap Wheel Adhesive,Epoxy Resin Flap Wheel Glue
Zhengzhou Jiading Abrasive Manufacturing Co.,Ltd , https://www.jd-abrasives.com