The first stage (1903-1919), wood and cloth structure;
The second stage (1920~1949), aluminum and steel structure;
The third stage (1950 ~ 1969), aluminum, titanium, steel structure;
The fourth stage (early 1970 to the beginning of the 21st century), aluminum, titanium, steel, composite structure (mainly aluminum);
The fifth stage (from the beginning of the 21st century to the present.): composite materials, aluminum, titanium, steel structure (mainly composite materials).
The development of composite materials in the aerospace field has experienced four stages of sub-loading members—the main bearing members of the tail-level—the main bearing members of the airfoil—the main components of the fuselage, gradually moving from small components to large core components, from military to civilian development. In Europe and the United States, the 1960s was the research and development stage of composite materials. In the 1970s, it entered the application stage. Since then, the proportion of composite materials used in aircraft has gradually increased.
Military aircraft
As an emerging material technology, composite materials are first used in military aircraft.
In the 1960s, glass fiber reinforced composites were first applied to the fairings and ailerons of aircraft. At this time, the mechanical properties of the composite material are still relatively low, and the aircraft parts manufactured by the composite material are small in size and small in force level.
In the late 1960s, boron fiber/epoxy composites began to be used in aircraft structures. For example, F-14 began using boron fiber reinforced epoxy composites on flat tails in 1971.
In the mid-1970s, high-performance composite materials with carbon fiber reinforcement were born, which opened up the large-scale application of composite materials on aircraft. Carbon fiber reinforced composites with excellent high specific strength, high specific modulus, corrosion resistance and fatigue resistance are ideal for aviation equipment. The heavy-duty and flat-sized parts of the military aircraft began to gradually use carbon fiber reinforced composite materials such as F-15, F-16, Mig-29, Mirage 2000, and F/A-18. Material tail, vertical tail. From the 70s to the present, foreign military aircraft tails have all adopted composite materials. The flat tail and vertical tail of the composite material generally account for 5%-7% of the total structural weight of the aircraft.
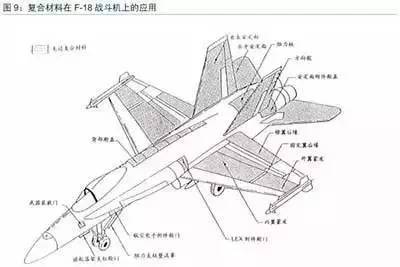
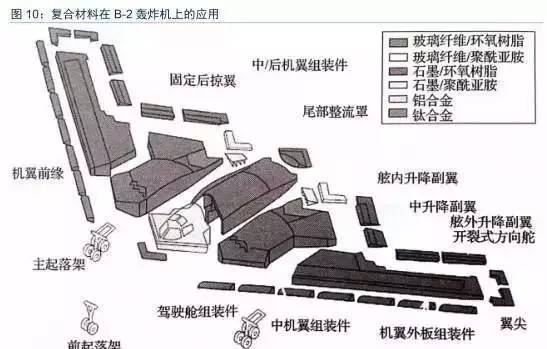
2. Civil aircraft
Civil aircraft is more concerned with the safety and economy of the aircraft, so it is more cautious in the application of composite materials. However, with the advancement of composite technology and the reduction of manufacturing costs, civil aircraft began to use composite parts gradually in the 1970s. Similar to military aircraft, the components of civil aircraft composite materials also develop from small bearing members to main bearing members.
In the United States, for example, the application of composite materials in civil aircraft has probably gone through four processes.
In the first stage, in the mid-1970s, composite materials were mainly used on components such as the leading edge, the flap, the fairing, and the spoiler.
In the second stage, in the mid-1980s, composite materials were mainly used in components such as elevators and ailerons that were less stressed.
In the third stage, the composite material is applied to components such as vertical tails and flat tails that are subjected to large forces. For example, the vertical tail and flat tail of the Boeing 777 aircraft are made of composite materials, and the composite material accounts for 11% of the total weight of the structure.
In the fourth stage, the composite material was applied to the wing and fuselage of the most important parts of the aircraft. The Boeing 787 Dreamliner uses 50% composite material, which exceeds the sum of the weight of metal materials such as aluminum, steel and titanium. Mainly used in the wing, fuselage, vertical tail, flat tail, fuselage floor beam, rear pressure frame and other parts, is the first large commercial aircraft with composite wing and fuselage.
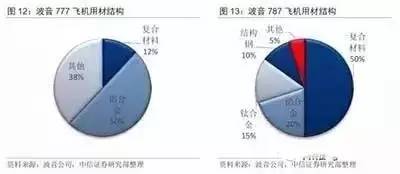
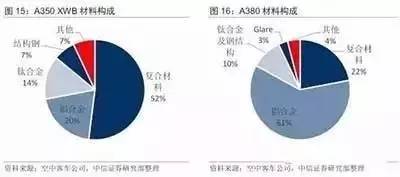
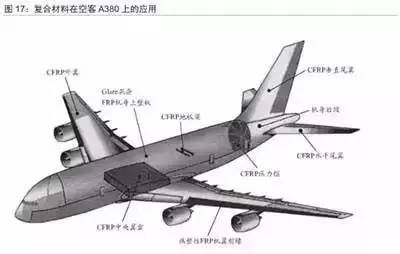
Helicopter
Helicopters are very significant for composite applications. Military, civilian and light helicopters use a large number of carbon fiber composite materials, and the amount of helicopter composite materials has reached 40%-60% of the structural weight. For example, the US helicopter gunship Comanche (RAH-66) uses 50% composite material; the European NH-90 helicopter uses 80% composite material, close to the all-composite structure.
The V-22 rotorcraft is a new type of flight structure that can take off and land vertically. After tilting the rotor, it can cruise at high speed. The composite material usage is 51%, including the fuselage, wing, tail, and rotating mechanism. Made of materials, it is also an all-composite aircraft.
4. Drone
Military drones have an urgent need for weight reduction, so composite materials are widely used in drones. For example, the US X-45 series aircraft uses more than 90% of composite materials; the X-47 series aircraft are basically all-composite aircraft, and the Global Hawk unmanned reconnaissance aircraft uses 65% of composite materials, including wings and tails. The rear fuselage, large radome, etc. are all made of composite materials; the European experimental drone "barracuda" and the US long-range attack drone "skunk" are basically the same.
5. Aero Engine
The amount and proportion of composite materials has also become a measure of the advanced level of aerospace engines. According to the different working temperature of the hot and cold end, the aerospace engine is correspondingly applied with a composite material of a plurality of different substrates.
The superior specific strength and specific modulus properties of resin-based composites are important for high-ratio aviation engines to reduce weight, improve propulsion efficiency, reduce noise and emissions, and reduce costs. They are mainly used on cold-end components of aircraft engines. The working temperature is below 150-200 °C, such as turbofan engine compressor blades, guide vanes and their frame components, turbofan nose cone and rectifying device.
Metal-based, ceramic-based, and carbon/carbon composites have important applications on hot-end components due to special conditions such as high temperatures.
SiC long fiber reinforced titanium matrix composite (Ti-MMC) has the advantages of high specific strength, high specific stiffness, high temperature resistance, good fatigue resistance and good creep performance. Ti-MMC leaf ring can replace parts of compressor disc. Lose weight by 70%.
Future aerospace engine compressor blades and mirror blades, integral leaf rings, casings and turbine shafts will all be manufactured from metal matrix composites. Ceramic-based composite materials have always been the focus of high-temperature materials research. The engine parts made of fine ceramics and silicon nitride can work at 1371 °C, and the performance is even better than that of high-temperature alloys.
But the problem of brittleness is still unresolved.
The carbon/carbon composite material also has the advantages of low density, high specific strength, high specific modulus, good thermal shock resistance, etc. It is the only candidate material at the working temperature above 1650 ° C, and the highest theoretical temperature reaches 2600 ° C, which is considered to be the most Promising high temperature materials.
6. Other defense industry
The high specific strength, high specific modulus and designability of composite materials make composite materials also have important applications in the non-aerospace defense industry.
Fiber reinforced composites have the characteristics of heat release, heat insulation and high temperature resistance, and are widely used in the aerospace industry.
For example, in terms of heat protection, the high-strength glass fiber resin-based composite material can be used as a multi-tube long-range rocket and air-to-air missile structural material and an ablation-resistant thermal insulation material, thereby realizing the integration of the nozzle converging section, the expansion section and the tailfoil. , greatly reducing the quality of weapons and improving tactical performance.
On satellites and spacecraft, the satellite structure quality in the United States and Europe is less than 10% of the total mass due to the widespread use of advanced composite materials. At present, satellite microwave communication systems, energy systems and various supporting structural members have basically achieved composite materials.
Carbon fiber composites have also been well applied in solid rocket motors. The "Pegasus", Delta launch vehicle, "Trident" II, and "Gnome" missile models all use composite solid rocket engines. The US strategic missile MX missile and the Russian strategic missile "Baiyang" M missile have adopted the launching tube of advanced composite materials.
Ship composite technology has also developed rapidly, and has basically reached the practical application level. Simplifying manufacturing and reducing costs have become the focus of current technology. US Navy equipment has been heavily used in composite materials such as the "Ford" aircraft carrier, the "Virginia" class submarine, and the DDG1000 destroyer. The British Navy's Type 45 destroyer also installed a comprehensive mast of sandwich composites, with stealth and reduced antenna maintenance; the British "smart" class submarine pump propellers also use fiber-reinforced foam sandwich composites.
Steel tape passes ROHS,En-71 and 6P environmental testing of Europe and the United States, it is non-toxic and tasteless, with characteristics of high temperature resistance, and good acid-alkali corrosion resistance.
Customized steel tape is our strength. We ensure that we can make the one suitable to your needs. Steel Tapes for Aggressive Industrial Applications, Machine Tools, Corrosive and Hi-Temperature labeling applications. Labels for component, equipment, safety and general labeling applications.
Feature
- Stainless Steel/Metal Steel labels have excellent resistance to chemicals, extreme weather conditions, high and low temperatures and abrasion.
- Inexpensive Durable Embossing Technology.
- Ideal for marking pipelines, underground cables, engine parts, building materials and machinery.
Quality 65Mn Steel Tape Measure Strip is environmental-friendly that passes ROHS,En-71 and 6P green test and meets the green standard of Europe and United States, featuring excellent resistance to chemicals, extreme high and low temperature and abrasion.
The production material of tape measure is sold in bulk. Wintape also provides customized service. The regular parameter is shown in below chart.
65Mn steel tape can pass Europe and the United States ROHS,En-71 and 6P (without phthalate) environmental testing, it does not contain any chemical composition, non-toxic and tasteless. High temperature, corrosion, acid and alkali.
Advanced CNC spring machinery, grinding and shot peening machinery,Precise tensile strength testers, and magnetic powder flaw detectors
Stainless Steel Leaf Spring,Stainless Steel Springs For Toys,Spring Constant Stainless Steel
Wintape Measuring Tape Company , https://www.wintapetape.com