Wellard Head Engineering in Aberdeen has been serving the oil and gas industry for 18 years and they have invested in the DMG MORI DMU 95 monoBLOCK ® machining center to provide better service and expand into new markets.
Mike Coutts, general manager of the company, said: "We manufacture complete sets of downhole tools, wellheads and winch equipment, and manufacture them according to the customer's design. In addition, we also provide personalized repair services. Investing in a 5-axis machining center has improved our core business. Our competitiveness allows us to better develop new markets. Now we are the only company in the north of Glasgow that has DMU 95 monoBLOCK ® . We held a customer open visit day, and our customers responded enthusiastically to our new 5-axis machining center. And they are welcomed. We expect this machine will promote the further development of our business."
The company has two Maho MH800 machining centers, all of which have been in existence for more than 12 years. The reliability of these machines is unmatched, so when the company buys machine tools, they need high-quality machines, and DMG MORI is their preferred supply. Business.
In the decision-making process, Wellahead was impressed with the level of knowledge of DMG MORI sales and technical staff who helped Wellahead select the right model based on the type of work and investigate the best match. Mike Coutts said: "Our main machining task is a cylinder, so we require a 26" 3-jaw chuck, which saves us a lot of fixtures. The machine's chuck, 5-axis machining capability, Siemens CNC system and unique machining cycle and in-machine laser tool setter limit the number of clamping times to less than 2 times, and set and program time is reduced by half. "In the past, when machining parts, multiple turning, milling and boring were required on different machines. The DMU 95 monoBLOCK ® concentrated all of this machining on this machine. Mike Coutts added: "We visited DMG MORI Factory, we see advanced engineering technology and manufacturing quality, we need the flexibility of the machine. We invested in another 3-axis machine, but the processing capabilities of the DMU 95 monoBLOCK ® offer us new opportunities. DMG MORI's technical support provides us with new processing methods and new cycles to increase our productivity. â€
The machine's high-rigidity makes full use of the full cutting edge of the 60 mm corn milling cutter without vibration. The company's old machine tools lack the torque required for such heavy-duty machining. Mike Coutts said: “We bought high-quality tools and we found that not only the tool life was extended, but the machining speed was also faster. The high-pressure coolant inside the tool allowed us to easily wash the chips during deep hole machining.†For example, there is a The part has 12 holes, and the previous hole requires 7 minutes of drilling. The DMU 95 monoBLOCK ® processes all 12 holes in just 7 minutes, and the U-shaped drill bit is drilled directly, eliminating the need for boring and requiring only 11% of the machine power.
DMG MORI places great emphasis on the transparency of the service, and the service hotline team answers and resolves customer questions. Response time and repair time are continuously and rigorously monitored. Now 96.75% of the calls can be received within 1 hour, and the service hotline can solve 39.92% of the problems on the phone, and it is free. For MORI products, the response time of the engineer's on-site service is only 0.9 days, and the DMG product is only 1.5 days. More importantly, 58.75% of the faults can be eliminated for the first time. DMG MORI is working to compress this time for all products to 1 day or less. In addition, high standards of after-sales service guarantees a well-planned pre-installation logistics and training program.
Wellahead has highly qualified engineers and trains the workforce through apprenticeships. Two of the engineers took part in the DMU 95 monoBLOCK basic training and the additional training ®. One of the students, Sam Morson, said: “DMG MORI answers all our questions, not ignoring them. The after-sales support is also excellent, the people we contact are very friendly and easy to interact with.†Mike Coutts added: “Before installation The inspection is very detailed, we ensure that we are ready to receive the goods, all the services are in place, the whole receiving process is very smooth. We arrange investment every two years, if we can verify other machines by work, we will invest without hesitation Buy a DMG MORI machine."
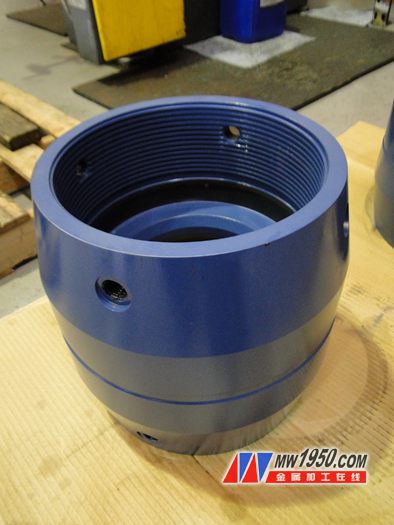
DMU 95 monoBLOCK ® produces parts for the oil and gas industry
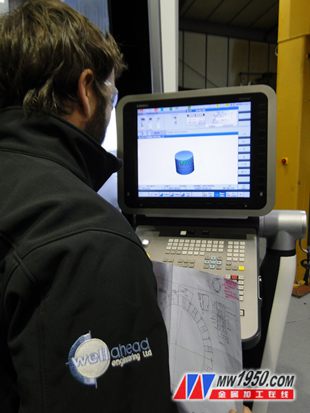
Operating the DMU 95 monoBLOCK ®
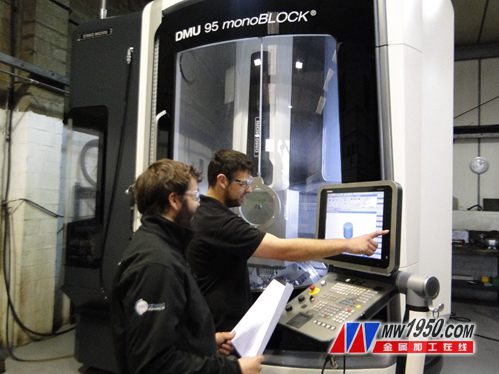
Operating the DMU 95 monoBLOCK ®
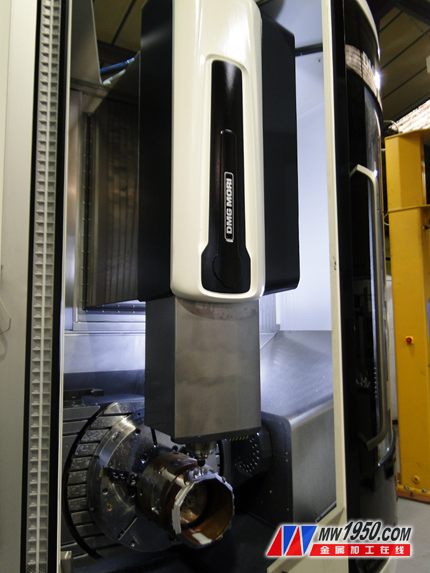
DMU 95 monoBLOCK ® rotating table
The endless stainless steel wire rope is made of multiple fine steel wires, which are connected end to end to form a closed loop. Mainly used to make annular Diamond Wire, widely used in the cutting of superhard materials such as silicon ingots and precious stones.
Stainless Steel Wire Rope,Stainless Steel Loop Saw,Stainless Steel Wire,Stainless Steel Rope
Jiangyin Baoneng Precision New Material Co.,LTD , https://www.baonengwire.com