introduction <br> é’½ is a kind of refractory rare metal with good plasticity and easy processing and processing. It is widely used in chemical industry, aerospace industry, nuclear energy industry and electronics industry [1]. In industrial production, é’½ structural parts are usually processed by welding, but there are problems such as suction, coarse grain and easy formation of pores and cracks in the welding process [2, 3], and its special application environment. The welding quality is very high, so ensuring the welding quality has become an urgent problem to be solved. The available data show that the research on the welding forming of niobium is still very lacking, so it is of practical significance to carry out research on the welding process. The welding process is a process of local rapid heating to high temperature and subsequent cooling. The temperature of the whole weldment changes sharply with time and space, and it is easy to form an uneven temperature field with large gradient in time and space. The distribution of temperature field determines the welding. The extent of the seam zone and the heat affected zone has a direct impact on the quality of the welded joint. In the actual industry, the flat butt welding process, due to the mechanical error of the fixed fixture and some human factors, can easily make a small gap between the butt workpiece, and the small gap has a great influence on the temperature field of the workpiece. At present, the research on welding temperature field calculation is limited to veneer remelting and gapless butt welding [4], and the existence of gap is an important factor affecting the quality of weld formation and welding. Therefore, research on this aspect is of great significance.
1 Calculation model and boundary conditions 1.1 Calculation model In this paper, the finite element analysis software ANSYS710 is used to numerically process the model. In the calculation process, the solid element so1id70 is combined with the surface unit surf152, in addition to the external and external convection heat dissipation conditions. Heat transfer between the workpiece and the fixture and the protection of the tire. Because of the symmetry of the model, only one test plate in the butt welding experiment was selected for modeling calculation. In order to ensure the docking gap, a special fixture is used to fix the workpiece to the working platform in the process performance test, and the workpiece size is 20 mm × 50 mm × 015 mm. In the welding test process, the self-made reverse surface protection tire is used to protect the workpiece with double-sided gas protection: the front shielding gas is helium gas, the gas flow rate is 7 L/min, and the reverse shielding gas is argon gas, and the gas flow rate is 5 L/min. Welding current I = 75A, welding voltage U = 1714 V, arc length 2 mm. Based on the ANSYS adaptive meshing technique, this study uses the meshing principle of tetrahedral and hexahedral elements to mesh the workpieces and fixtures with different element shapes. The model uses a non-uniform grid approach to partition the cells. As shown in Figure 1, a relatively fine mesh is used in the abutting and near-slit areas, and a coarser meshing is used away from the weld area. This allows for both calculation accuracy and speed.
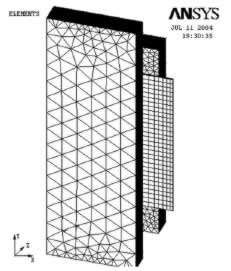
1.2 Heat source loading The thermal energy distribution in the arc heating zone is in the form of a near-actual Gaussian distribution. The heat flux distribution at any point r(x, y) within the arc heating radius is given by equation (1) [6].
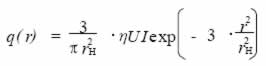
Where: η represents the heating efficiency, taken here 017; U is the arc voltage; I is the welding current; rH is the radius of the spot heating zone.
1.3 Handling of boundary conditions 1) Initial conditions at the moment of arcing:
2) When calculating, set the abutting surface at the gap as the convection boundary, and consider the convective heat dissipation when the air circulates at the gap with the workpiece. Workpiece and air heat exchange convection boundary conditions:
In the formula:
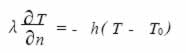
Indicates the temperature gradient in any direction on the workpiece; λ is the thermal conductivity of the material; h is the convection coefficient of the material.
2 Calculation results and analysis 2.1 Influence of the butt gap on the surface temperature field of the workpiece In order to analyze the influence of the existence of the mating gap on the temperature field of the workpiece, the modeling of the gap between 0109 mm and the absence of the gap is carried out. Two boundary conditions, convection and conduction, are used. The calculation results show that when there is no docking gap, the shape of the surface of the molten pool is circular, that is, the x direction is equal to the width of the y direction; when the mating gap exists, the surface shape of the molten pool is elliptical, that is, the x direction and the y direction are different. This is because the convection heat dissipation velocity at the abutting surface is slow when the butt gap exists, so that the isotherms are densely distributed in the x direction and sparsely distributed in the y direction, so the melting width in the y direction is larger than the melting width in the x direction. The effect is more pronounced as the welding time changes. Figure 2 shows the variation of the width of the weld in the x and y directions with the weld time. The presence of the gap is a factor in the change in the shape of the molten pool. See Table 1 for the calculation results under the two boundary conditions.
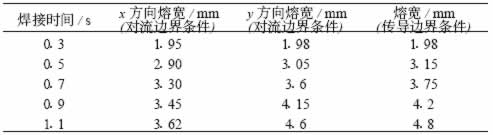
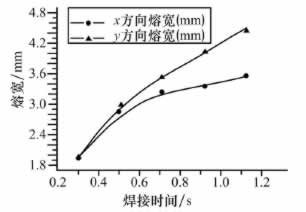
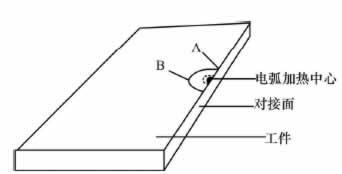
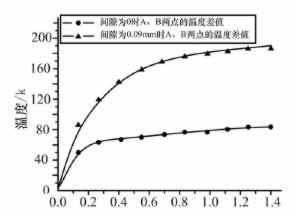
In order to further analyze the influence law of the gap on the temperature field distribution on the workpiece, the nodes with the arc heating center of 5 mm are selected on the abutting surface of the gap and the inside of the workpiece respectively. See Figure 3 for the schematic diagram of the selection method. In order to eliminate the influence of the heat conduction of the fixture on the temperature field at different positions on the workpiece, the change of the temperature difference between the two points A and B is calculated in the case of the presence or absence of the mating gap. Under the same conditions, the two conditions A and B The curve of the temperature difference of the point is shown in Figure 4. It can be seen from Fig. 4 that due to the influence of the heat conduction of the fixture, the temperature of the two points A and B has a certain difference; when the gap exists, the temperature of the workpiece butt surface rises rapidly due to the influence of the gap, and the temperature in the same time The value is much higher than the equidistant position in the workpiece. The temperature difference between the two points A and B is much larger than that without the mating gap.
2.2 Influence of different butt gaps on the surface temperature field of the workpiece When there is a gap between the two welded plates, the butt plate generates thermal convection with the surrounding environment, taking away some of the heat, thus reducing the temperature inside the plate. The size of the butt gap directly affects the effective range of the arc. The width of the gap in the x and y directions is calculated within the allowable range of the weld gap. The calculation results show that the width of the effective range of the arc varies with the gap. The larger and smaller, the difference between the width of the x-direction and the y-direction increases as the mating gap increases. Figure 5 shows the curve of the melt width as a function of the butt gap when the heat source is applied for 0125 s. When the position of the welding torch deviates from the center of the weld, the weld is poorly formed and the welding quality is affected. According to this, the temperature field on the workpiece is calculated when the gap is 011 mm and the welding gun is 0102 mm and 0108 mm respectively, and the corresponding deviation of the welding gun position on the two butt plates is the same. See Figure 6 for the temperature difference curve on the two butt plates after 1 s of welding heat source action. The calculation results show that if the welding gun deviates from the center of the weld, if there is no mating gap between the two plates, the temperature distribution between the two plates is not obvious due to the strong conduction heat transfer between the two plates. When the butt gap exists, the gap is The edge effect and the heat transfer effect caused by the effective range of the welding heat source are different, which makes the temperature distribution on the two plates greatly different, especially the difference in temperature peak value. In this calculation, the temperature peak difference is when the welding torch deviates from 0106 mm. The value is around 200 K, but this temperature difference is not obvious away from the welding heat source.
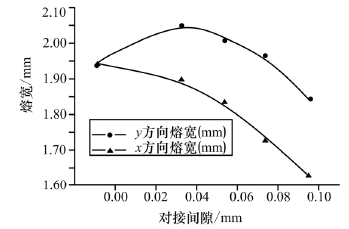
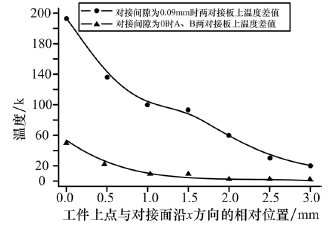
3 Conclusion <br> This paper analyzes the effects of different docking gaps on the welding temperature field. The model established in this paper is verified by welding process test. The results show that the established model is correct, and the numerical calculation method is feasible. The calculation results are similar to the experimental results. And get the following rules:
1) The existence of the gap makes the temperature field unevenly distributed, which is a decisive factor for the shape of the surface of the molten pool to be elliptical. This effect is more obvious with the increase of welding time.
2) Under the same conditions of other welding process parameters, the size of the mating gap determines the effective range of the arc. As the mating gap increases, the width of the gap decreases, and the width of the X-direction decreases compared with the Y direction. Much more obvious, this effect makes the surface morphology of the molten pool more obvious.
3) When the welding torch deviates from the center of the weld, the edge effect caused by the mating gap makes the temperature difference between the two butt plates much larger than when there is no gap, which makes the difference of the size of the molten pool on the two plates obvious, resulting in poor weld formation. It is required that the position of the welding torch should be strictly aligned during the TIGæ°¦ arc welding process to ensure the welding quality.
Compared with single-channel pipettes, multi-channel pipettes simplify all the tasks associated with microtiter plates that often occur in immunology, biochemistry, clinical diagnosis and food analysis. Multi-channel pipettes generally have 8 and 12 heads. The gun body can be rotated at 360°C, and each part can be disassembled and repaired separately. The lower half can be sterilized at 121°C. The dimpled housing ensures a firmer grip for the operator. Can be quickly calibrated.
how to use multi channel pipette,best multi channel pipette,multi channel pipette for 384 well plate
Yong Yue Medical Technology(Kunshan) Co.,Ltd , https://www.yonyuemedicals.com