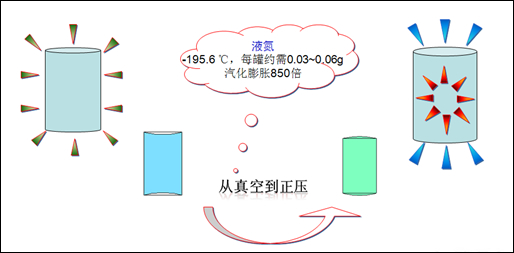
The formal freight elevators are those that can push cattle or even forklift. The speed is generally 0.5m/s, and the load is larger, including 2t, 3t, 4t and 5t. Due to the need to enter the forklift truck, the floor sill is of reinforced type. The rear wall of the car should preferably be equipped with a crash plate, and the car bottom should be steel plate. The load of the freight elevator is very large, and the height and width of the door opening are generally made to be consistent with the height and width of the car as much as possible. Then the call button panel in the car is on the side car wall.
Cargo Elevator,Cargo Lift Elevator,Cargo Elevator Lift,Small Cargo Elevator
Suzhou Stable Trade Co., Ltd , https://www.stable-elevator.com