The race lights went out, the game started, the full gear, the 230-horsepower engine made a roar like roar, the racer stepped on the throttle and lean forward, and the speed reached 165 km/h after 2.6 seconds. After 5 seconds, BMW's new SUTER is flying like a thunder on the asphalt track at a speed of 200 kilometers per hour. This speed is enough to make any Porsche racer feel shocked, because to achieve this performance, for racing drivers and motorcycle racing, must reach a very high standard. Racers have to work harder than ordinary people, and the car must be equipped with a high-quality system to ensure its high speed and safe operation.
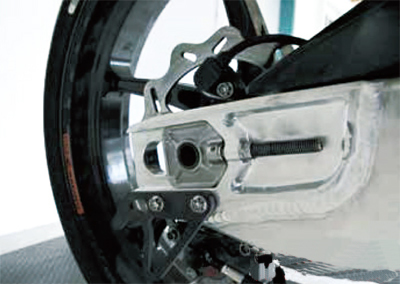
Rear axle of motorcycle Moto3: screws and nuts made of titanium alloy
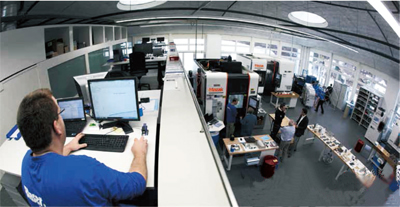
300 m2 technical center at the Bassou headquarters in Hasle-Ruegsau, Switzerland
Mr. Roger Sutter, a Swiss manufacturer of SUTER motorcycle racing, explained that the biggest challenge for us is how to ensure the strength, speed and safety of the car while the body is lighter. "We must calculate the weight for the weight," adds it. In order to achieve this balance, the use of titanium alloys to make motorcycle racing will be the general trend. “Titanium has the advantages of good rigidity and light weight, but lightweight metal is a difficult material to process. How to find a tool that can process this material efficiently is a big difficulty for us.†Swiss KAISER Precision Tool Production Director Mr. Hansueli Looser added, “We are getting more and more complaints from customers about the processing of titanium or Inconel. Customers complain that the tool life is so short, it is unacceptable.†“Cause this The main cause of the result is the vibration generated during the machining process. In fact, the solution is very simple,†says Hansueli Looser. As long as the tool is perfectly combined with the cutting fluid, tool life can be extended when machining difficult metals such as titanium alloys. And shorten the processing time. That is to choose the anti-vibration tool, find the best blade, you can reduce the wear, and choose the right titanium alloy machining fluid for processing and cooling, which can minimize the friction and improve the processing quality.
So far, there have been few related studies in the processing of titanium alloys, so many manufacturers have the same problems, but there is no solution to this:
In fact, Swiss Basso Lubrication Co., Ltd. has studied in this field. For manufacturers, the cost of tools and metal cutting fluids is only a tiny fraction of a new machine tool, so manufacturers don't focus on the huge impact of metal cutting fluids on workpieces and tools in different materials, and it's easy to underestimate the correct What is the impact of cutting fluid on the machining of workpieces, they believe that cutting fluid is only the devil that increases the processing cost of the enterprise during the cutting process. Christoph Wüthrich, Director of Technology Center at Basso Swiss Lubrication GmbH, stressed that in this industry, the choice of cutting fluid is crucial.
So far, there have been few related studies in the processing of titanium alloys, so many manufacturers have the same problems, but there is no solution to this:
In fact, Swiss Basso Lubrication Co., Ltd. has studied in this field. For manufacturers, the cost of tools and metal cutting fluids is only a tiny fraction of a new machine tool, so manufacturers don't focus on the huge impact of metal cutting fluids on workpieces and tools in different materials, and it's easy to underestimate the correct What is the impact of cutting fluid on the machining of workpieces, they believe that cutting fluid is only the devil that increases the processing cost of the enterprise during the cutting process. Christoph Wüthrich, Director of Technology Center at Basso Swiss Lubrication GmbH, stressed that in this industry, the choice of cutting fluid is crucial.
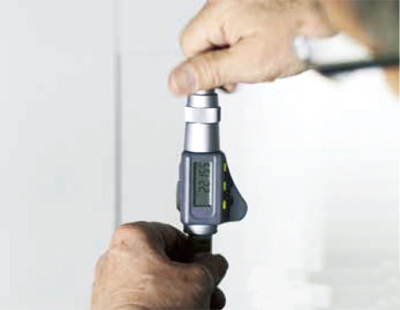
A total of more than 1200 drilling tests and assessments
Basso Technology Center
Let us walk into the technical center at the Basto headquarters in Hasle-Rüegsau, Switzerland, which will explain the importance of metal cutting fluids in the machining process and the impact on the machining process. According to Mr. Christoph Wüthrich, Technical Director, at the center of 300 square meters, Basso needs to conduct targeted tests according to the customer's processing technology and workpieces. Such research tests are as hard as "finding a needle in the grasshopper". Because different performance metal cutting fluids are formulated with different additives.
Titanium alloy processing test
The metal cutting fluid company from five different brands and the products of several tool competitors were tested in KAISER, Switzerland. The blades of different manufacturers were matched with different brands of cutting fluid to see which combination will effectively extend the service life of the blade. All tests were performed on a titanium alloy workpiece specified by the manufacturer. The test results are exactly the same as the original judgment. The results of the different blades are quite different. Under the same conditions, the most suitable blade life can be increased by 20 times; and the best cutting fluid significantly extends the tool life. The winning combination: Basso's B-Cool755 and KAISER's 655.389 blade produce an extraordinary effect, the blade wear is only 0.002mm, the result is that after the completion of 81, 51mm deep pupil, the pupil speed is 120m / Min, and this speed belongs to high speed machining in titanium alloy processing.
Overview of test results
Choosing the right metal cutting fluid determines the life of the tool. For workpieces of the same material, the service life can be increased by a factor of 15. As for the blade, there is a dramatic difference, even with the same metal cutting fluid and cutting parameters, the tool life is still 20 times different. Titanium alloy boring best test combination: Switzerland KAISER 655.389 with Swiss Basso B-Cool755.
Let us walk into the technical center at the Basto headquarters in Hasle-Rüegsau, Switzerland, which will explain the importance of metal cutting fluids in the machining process and the impact on the machining process. According to Mr. Christoph Wüthrich, Technical Director, at the center of 300 square meters, Basso needs to conduct targeted tests according to the customer's processing technology and workpieces. Such research tests are as hard as "finding a needle in the grasshopper". Because different performance metal cutting fluids are formulated with different additives.
Titanium alloy processing test
The metal cutting fluid company from five different brands and the products of several tool competitors were tested in KAISER, Switzerland. The blades of different manufacturers were matched with different brands of cutting fluid to see which combination will effectively extend the service life of the blade. All tests were performed on a titanium alloy workpiece specified by the manufacturer. The test results are exactly the same as the original judgment. The results of the different blades are quite different. Under the same conditions, the most suitable blade life can be increased by 20 times; and the best cutting fluid significantly extends the tool life. The winning combination: Basso's B-Cool755 and KAISER's 655.389 blade produce an extraordinary effect, the blade wear is only 0.002mm, the result is that after the completion of 81, 51mm deep pupil, the pupil speed is 120m / Min, and this speed belongs to high speed machining in titanium alloy processing.
Overview of test results
Choosing the right metal cutting fluid determines the life of the tool. For workpieces of the same material, the service life can be increased by a factor of 15. As for the blade, there is a dramatic difference, even with the same metal cutting fluid and cutting parameters, the tool life is still 20 times different. Titanium alloy boring best test combination: Switzerland KAISER 655.389 with Swiss Basso B-Cool755.
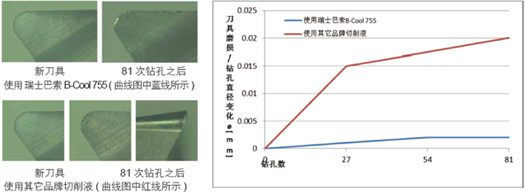
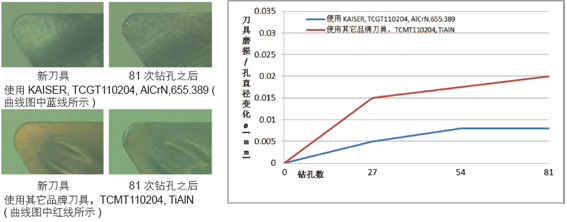
Graphic: Use Swiss Basso B-Cool755 with Swiss KAISER 655.389 tool and other brands comparison tool: KAISER, TCGT110201, AICrN, Art.Nr.655.389; Material: titanium alloy, Ti6A14V, 3.7164
Hole diameter: 21–26 mm; reaming depth: 51 mm; Vc: 120 m/min; fn: 0.1 mm/u
ISO9624 PN10 LAPPED FLANGE, DN15-DN10000, LOOSE FLANGE, S235JR, DN15-DN1000.
ISO9624 PN16 LAPPED FLANGE, DN15-DN10000, LOOSE FLANGE, S235JR, DN15-DN1000.
PN16 Flange,ISO Flanges,ISO Plate Flange,ISO Standard Flange
Shandong Zhongnuo Heavy Industry Co.,Ltd. , https://www.zhongnuoflanges.com