Model NO.: 1050, 1060, 1070, 1100, 3003, 3105, 5052, 5005
Brand Name: Signi Aluminium
Place of Origin: Zhengzhou China (Mainland)
Port of Loading: Qingdao,Shanghai
Trademark: Signi
Transport Package: Wooden Pallet
Specification: China Standard
Origin: China
HS Code: 76061190
Anodized aluminum coil sheet for architecture     Anodizing is an electro-chemical process to modify the surface of aluminum to create a hard and durable ceramic layer that is corrosion and UV resistant. The anodized surface is transparent, retaining the metallic appearance, and can be combined with colouring to offer a wide range of colour options.
Â
The advantages of Signi Anodized aluminum coil sheet for architecture
Â
1.Authentic metallic lustre and feel
The anodized layer is transparent and integrated in the surface of the metal; the natural metallic appearance and feel of the aluminum are fully preserved, the anodized finish will enhance and reinforce the natural beauty of aluminum to creat a living surface constantly interacting with the natural or artificial light playing across its surface.
Â
2.Excellent corrosion resistance
Even in its natural state, aluminum does not corrode in the same, destructive, way as iron and steel. Corrosion of aluminum, however, permanently damages the aspect of the metal. The natural oxide layer of aluminum provides a self defence against corrosion. However, this natural oxide layer of aluminum is thin, irregular and unstructured with only superficial corrosion protection. Anodizing creats a thick, perfectly formed and scientifically controlled oxide layer, which ensures a surface of unparalleled corrosion resistance and locks in the pure and natural metallic aspect of the metal. In particular, anodized finishes are highly durable in city and marine environments, due to their resistance to chlorides and sulphates.
Â
3.Proven durability + technical continuity
Â
The technology of anodizing has been established for almost 100 years. Whilst the proces has been continuously refined, especially in terms of quality, the chemical and technological fundamentals remain unchanged.
Â
The on-site behaviour of the anodized surfaces produced today is fully predictable, based on the proven, long term, service experience. Independent inspection commissioned by United Anodizers has confirmed that the anodized protection remains undiminished after more than 30 years.
Â
4.No risk of adhesion failure
Â
Anodizing is an eletrolytic process, which transforms the surface of the metal into an oxide layer integral with the metal itself. It is not a coating applied to the surface of the metal, therefore, no risk of adhesion failure such as peeling, blistering, cracking, splitting, or chipping with may occur with surface coatings, such as painting. There will be no adhesion failure, even on cut edge or joints.
Â
5.No possibility of fading
Â
Natural silver, bronze, anodized finishes contain no organic elements, therefore no colour fading is possible during the service life of these finishes.
Â
6.No possibility of filiform corrosion
Â
Filiform corrosion is an attack on the hidden inter-layer between the aluminum and the surface finish which results in the propagation of corrrosion under the surface finish. It cannot be remedied. It originates from surface defects, surface damage or scratches.
Â
7.No chalking
Â
Chalking is the formation of a fine powder on the surface of the paint film during weathering. It can cause significant deterioration in surface appearance, with a reduction in the gloss level, surfaces lustre and colour. Anodized aluminum does not suffer from this disfiguring condition, even when exposed to difficult exterior environmental conditions, such as marine locations or very sunny and or humid climates.
Â
8.Uniform surface finish for all metal shapes and textures.
Â
Anodizing is a process which can be carried out prior to or after the transformation of the metal. Since it is an electro-chemical immersion process rather then an applied finish, anodizing provides a particularly uniform an regular finish on most metal shapes and textured surfaces, such as perforated sheets, tread plates, linished or brushed metal, mesh material, stucco surfaces etc.
Â
9.Optimum coverage
Â
Anodizing, an an electro-chemical immersion process achieves a more uniform surface coverage, especially for extruded sections. With spray paint processes and, especially with powder-coating, the non-visible surface is often not coated.
Â
10.Highly imper meable anodized layer
Â
A properly sealed anodized layer is impermeable. An organic coating is always porous. Furthermore, when severe environmental temperature fluctuations occur, the anodized layer is not subject to damagin physical changes and consequential embrittlement.
Â
11.Abrasion resistance
Â
Aluminum oxide is a very hard compound which is second only to diamond, on the Mohs scale of mineral hardness. ANodized aluminum surfaces offer, therefore, superior scratch and abrasion resistance than coated surfaces.
Â
12.Guarantees
Guarantees are often considered by specifiers or building owners to provide reassurance about the long term performance of a surface finish.
Â
Specification-Anodized aluminum coil sheet for architecture | ||||||||
Alloy | Temper | Thickness (mm) |
Thickness Tolerance |
Width (mm) |
Width Tolerance |
Length (mm) |
Length Tolerance |
|
1050, 1060, 1070 ,1100, 3003, 3105, 5052, 5005,5154,5754, 5083, 5182, 6061, 6063,etc | O, F H14, H16,H18H32,H34 H36,H38 etc. Â |
≤3mm | Thickness tolerance is according to EN485-4 Standard | ≤1520 | Width Tolerance is according to EN485-4 Standard |
800-- 2600 Â |
Length tolerance is according to EN485-4 Standard | |
Anodized aluminum film: | ≤ 20 um, or as customer's request | |||||||
Surface: | Satin Finish,Bright finish, Brush finish,Sand etc. | |||||||
Colors: | Nature,Champagne,Gold,Grey,Bronze,Dark Bronze,Black,etc | |||||||
Mechanical properties are in complicance with EN485-2 standard |
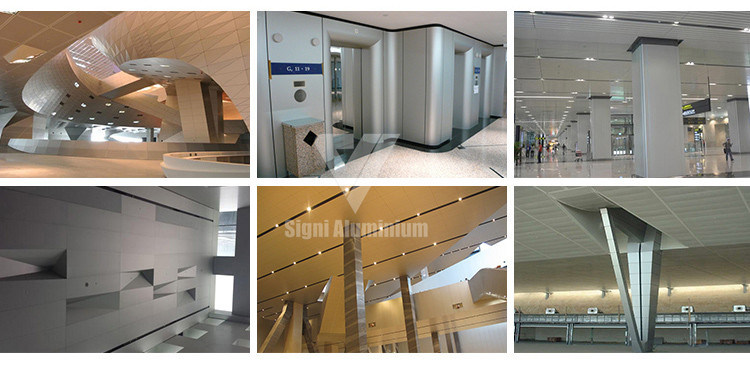
Â
Acid Printing Auxiliary Series
Pigment Paste,Dispersant,Fixing Agent,Surfactant Co., Ltd. , http://www.saltadditive.com